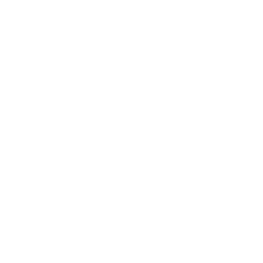
News
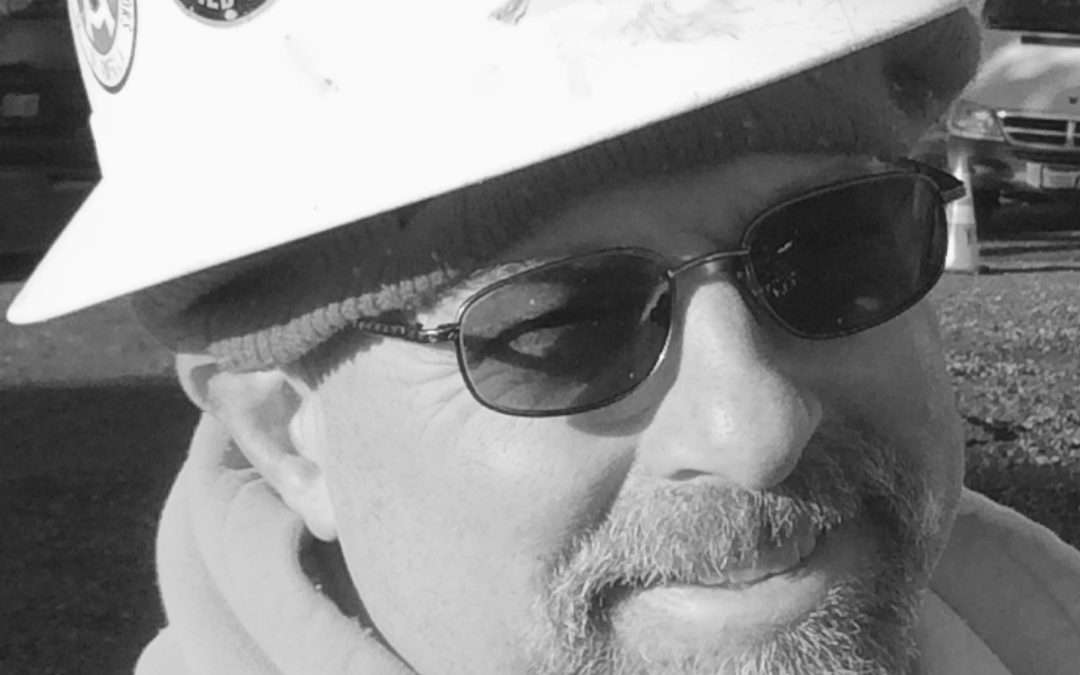
40 Years With Fisher And Counting
Rob Miller began his career with Fisher in April of 1984 working as an apprentice. As a leading Superintendent II, Rob is now in an elite class as he celebrates 40 years with Fisher Construction Group. Rob’s reputation precedes him. He has spent...
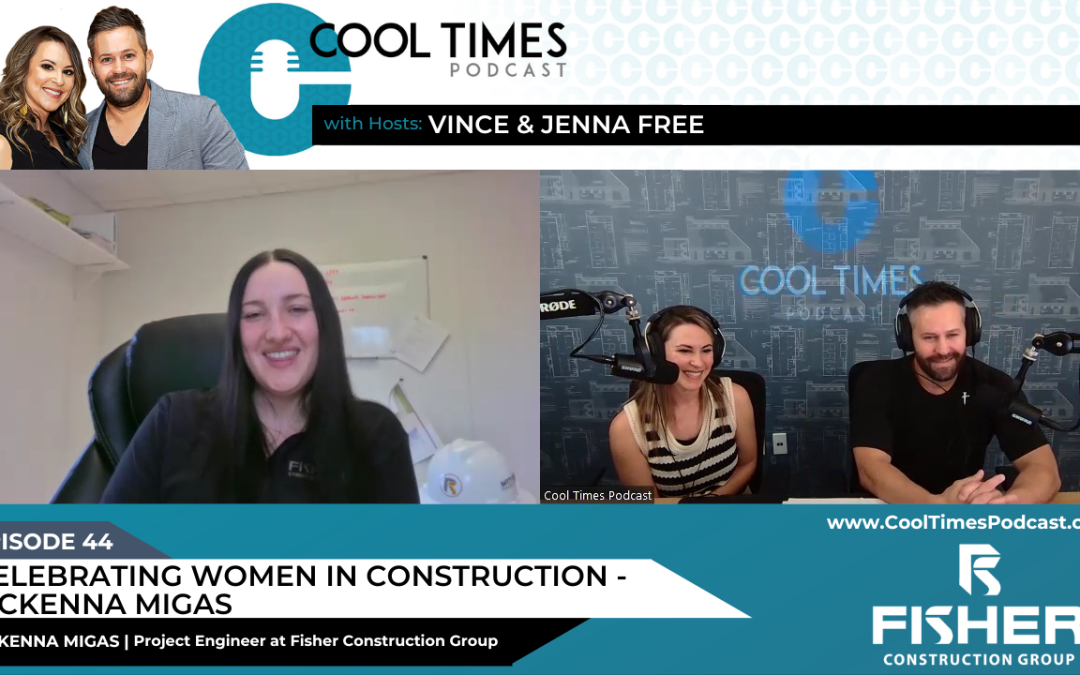
Fisher Featured on Cool Times Podcast
McKenna Migas, Project Engineer with Fisher Construction Group, Celebrating Women in Construction In this episode of The Cool Times podcast, hosts Vince Free and Jenna Free sit down with guest McKenna Migas, Project Engineer at Fisher Construction...
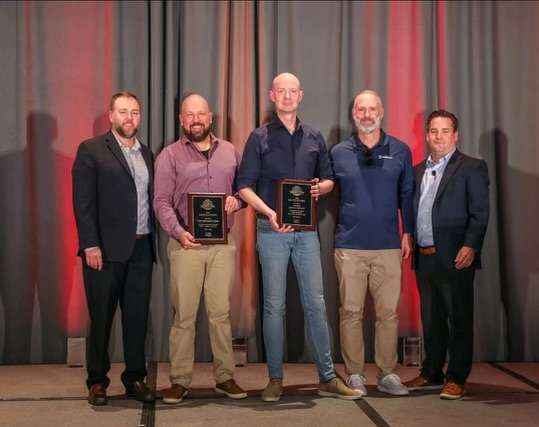
Fisher Wins the Built by the Best Award 2023
FOR IMMEDIATE RELEASE: November 14, 2023, Palm Springs, California Controlled Environment Building Association (CEBA) named Fisher Construction Group the winner of 2023 Built by the Best at the CEBA Conference & Expo in the Over $35MM Category...
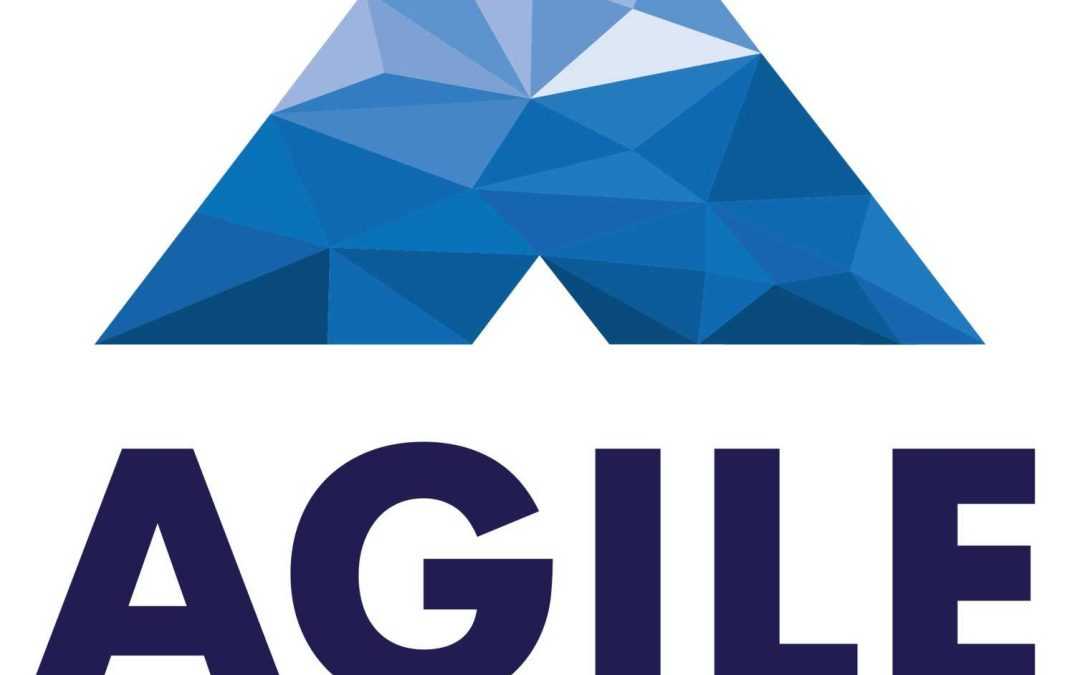
Agile Cold Storage Announces ASRS Expansion to Gainesville, GA Facility
Taking Agile Cold Storage to New Heights...
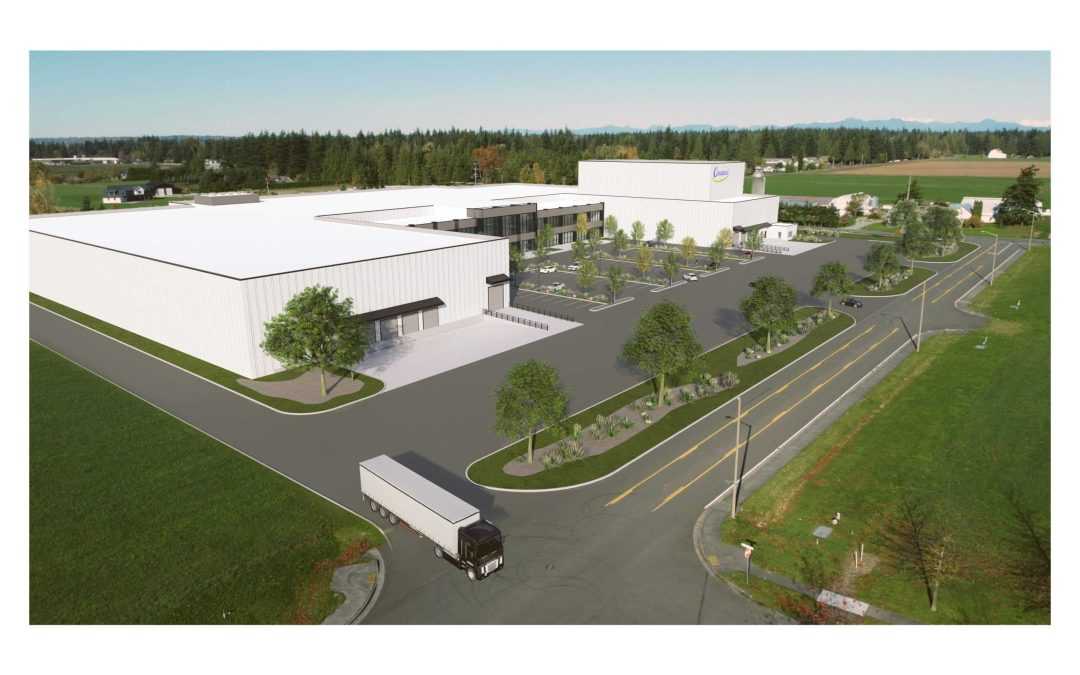
Alliance Freeze Dry Group Underway with Canature Kitchen Lynden Facility
FOR IMMEDIATE RELEASE: November 4, 2021, Las Vegas, Nevada - The Controlled Environment Building Association (CEBA), a Core Partner of the Global...
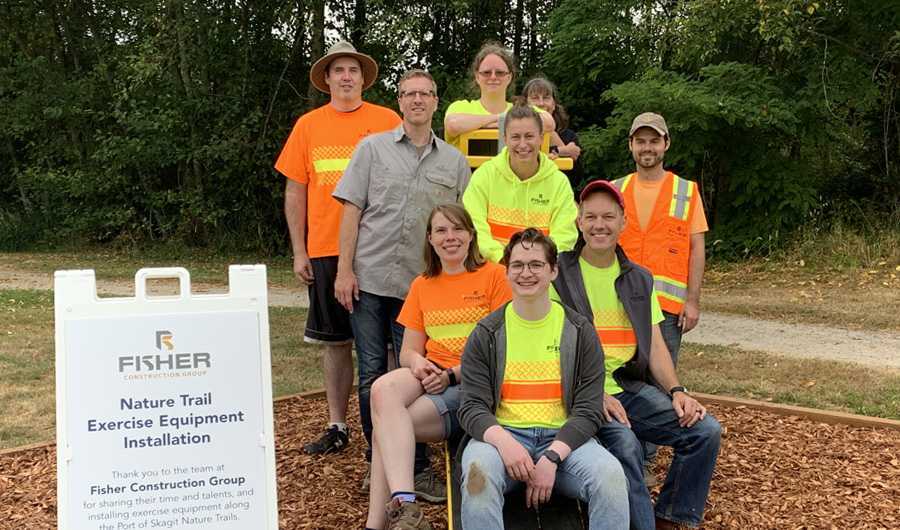
Giving Back is Part of Fisher’s A&E Team’s Mission
Fisher’s Architectural and Engineering team headed out to the trails last week to help improve the already much-loved trail system at the Port of...
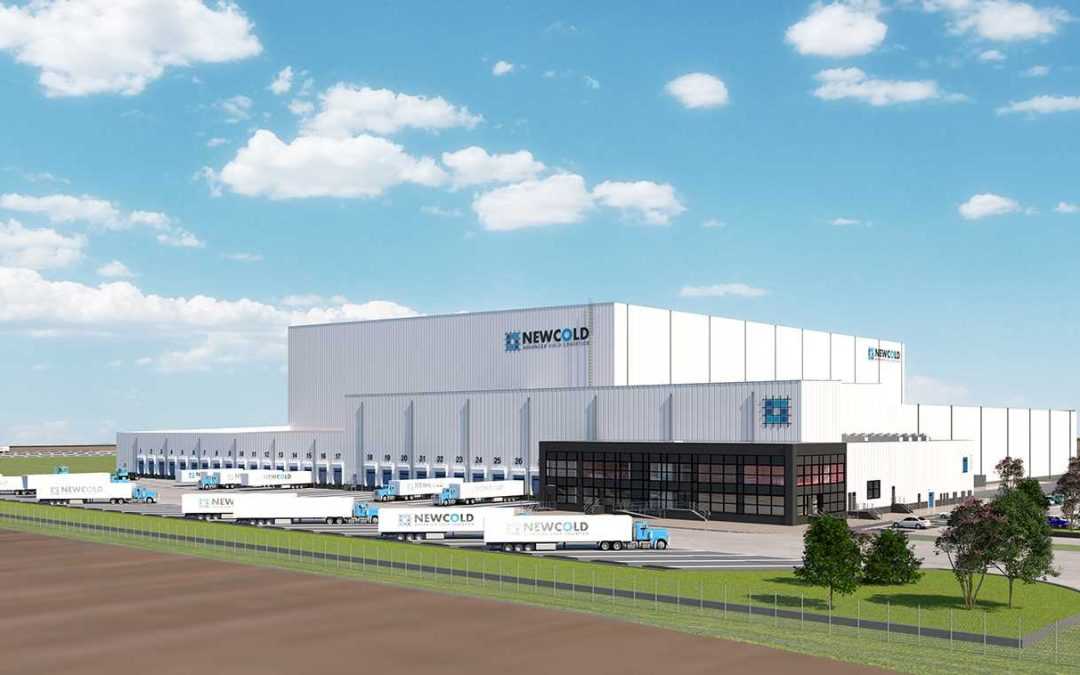
NewCold Project Underway Near Indianapolis
NewCold Continues to Transform the Cold Store...
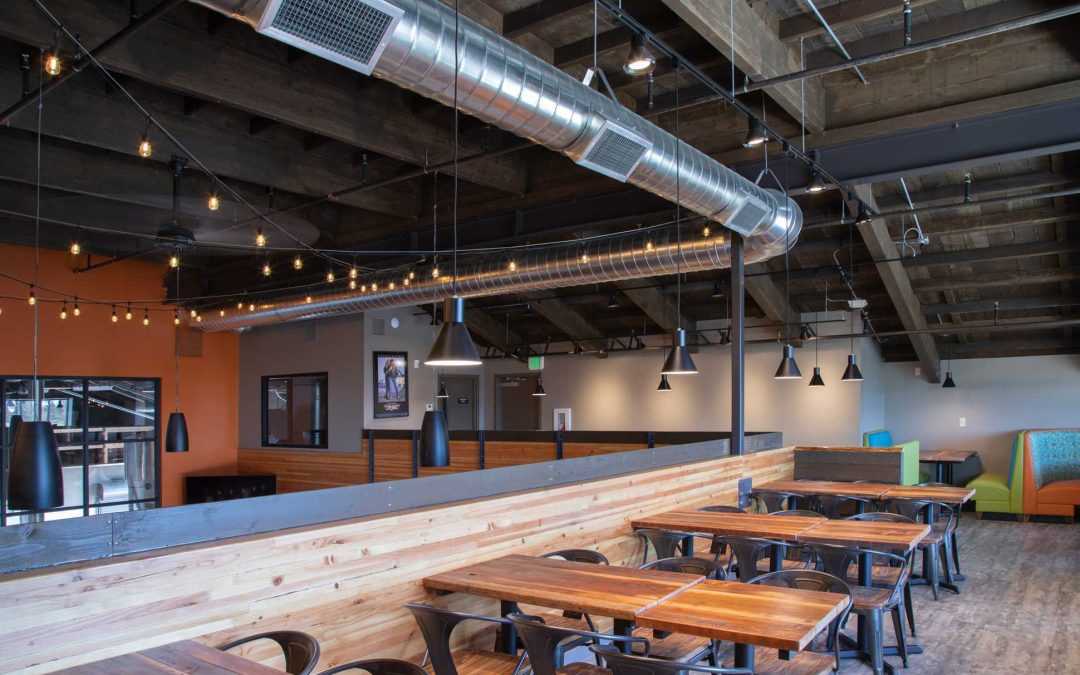
Fisher’s Project for District Brewing Wins Historic Preservation Award
If you grew up in the Skagit area, you probably...
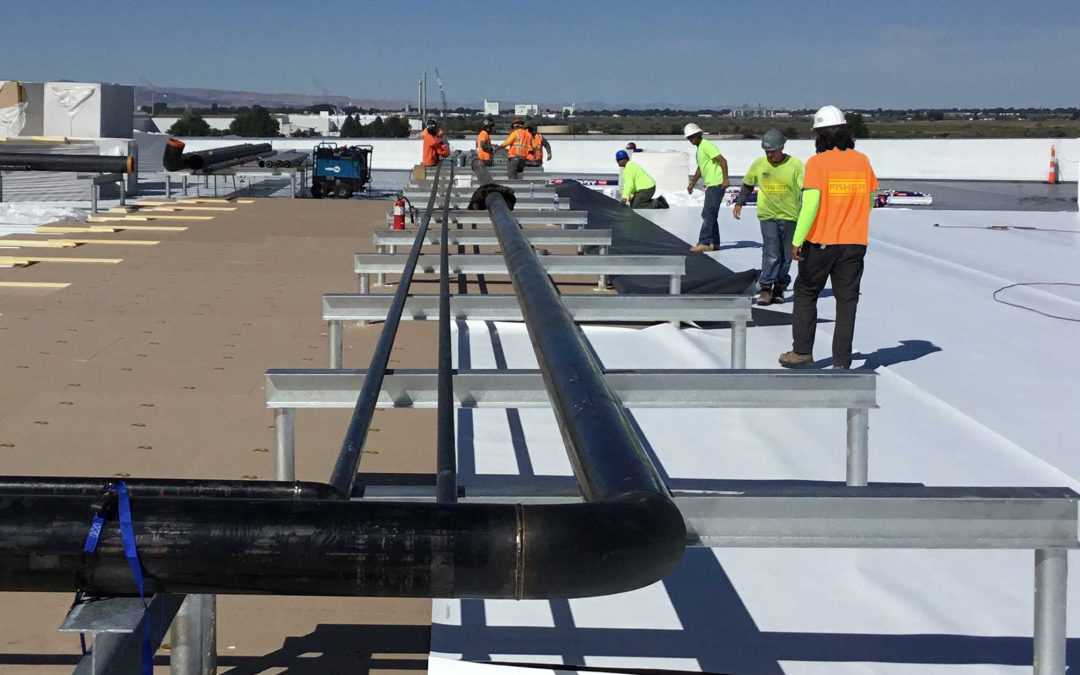
Fisher Construction Group Announces New Roofing Division
Fisher Construction Group has completed agreements...
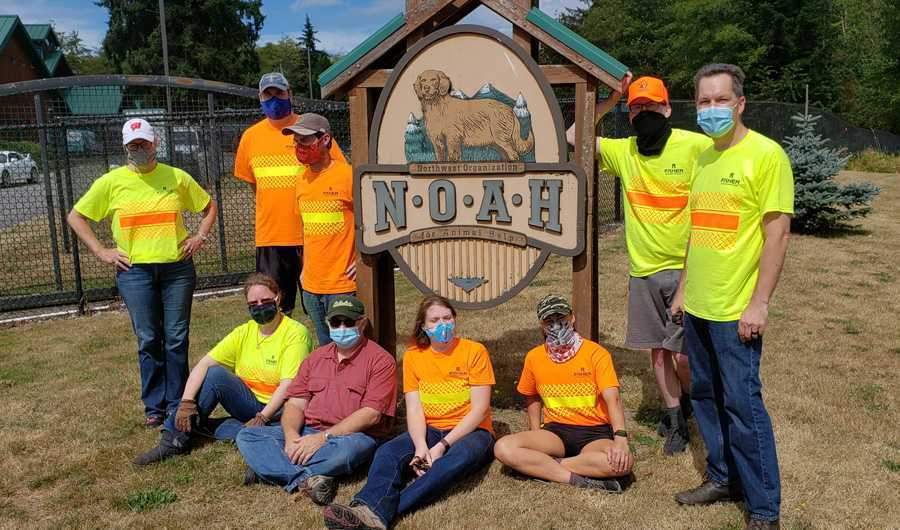
Fisher’s A&E Team Lends a Hand Developing Trail System at Animal Shelter
It is said a person has two hands. The first for helping themselves, the second for helping others. And every few months, Fisher’s Architectural...
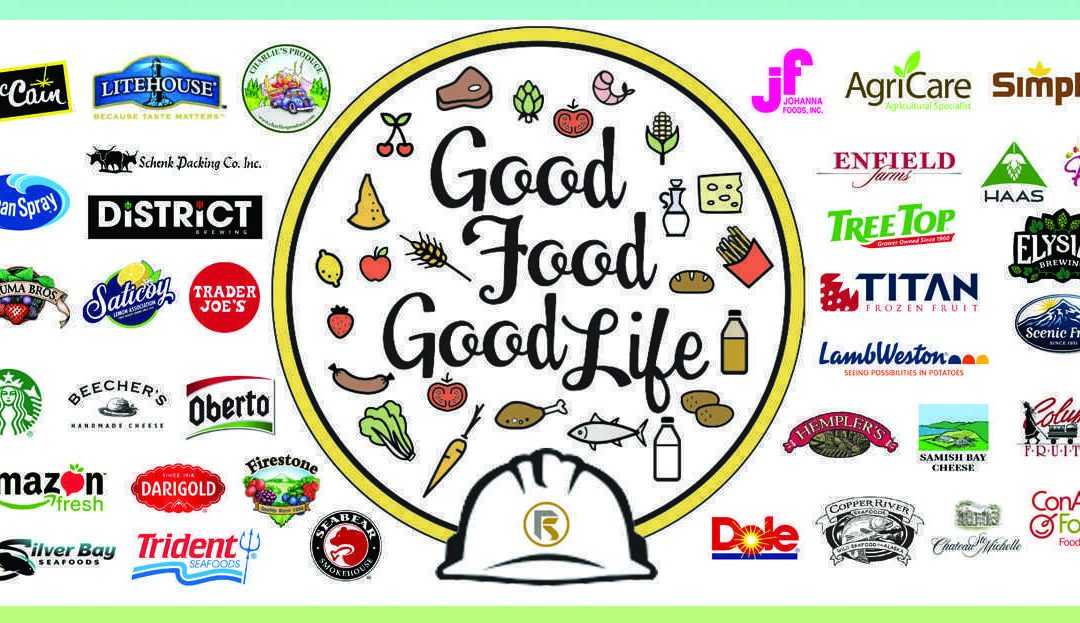
What’s Cookin’ at Fisher? We’re Serving Up Favorites Made with Our Client’s Products
It isn't a secret. We're big fans of the foods (and beverages) our clients produce. With the first holiday of summer coming up, we challenged our...
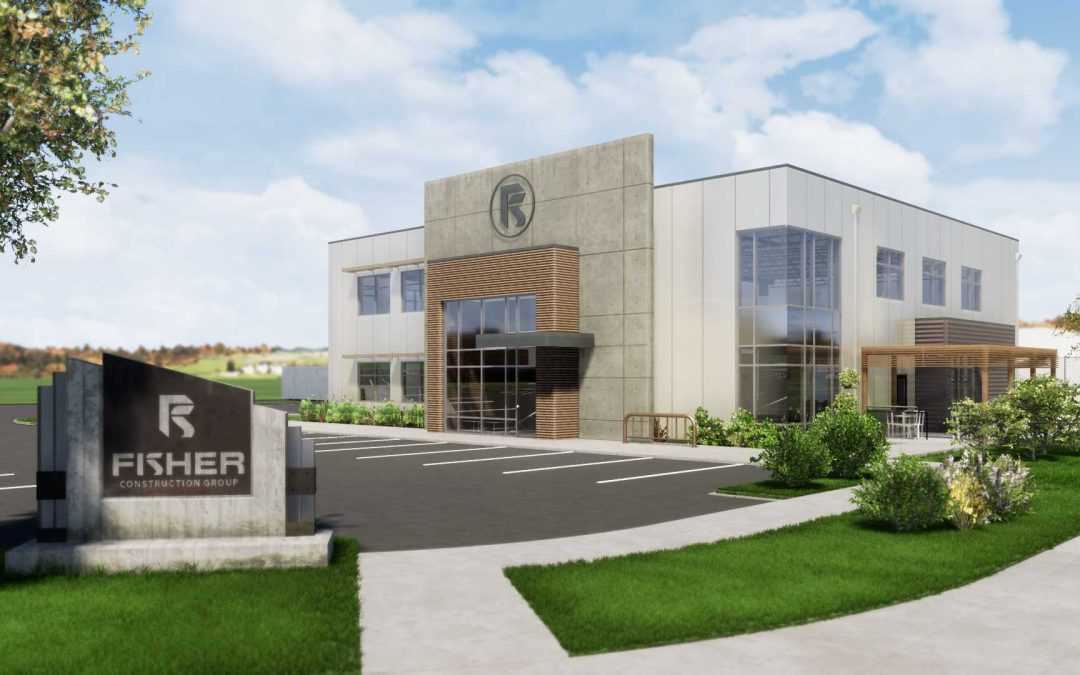
Fisher Moves Forward with New Office Building in Vancouver
Fisher Construction Group recently announced crews have began construction on a new office in Vancouver, Washington. The project is located at 3200...
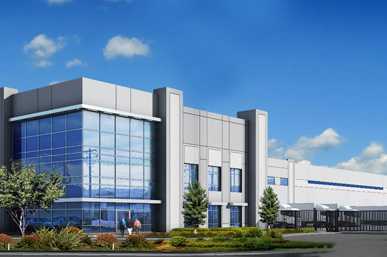
Construction Underway on CenterPoint Landing at Oakland Seaport
Fisher’s CenterPoint Landing project at the Port of Oakland is well underway since the final permit was approved in mid-July. Over the last year,...
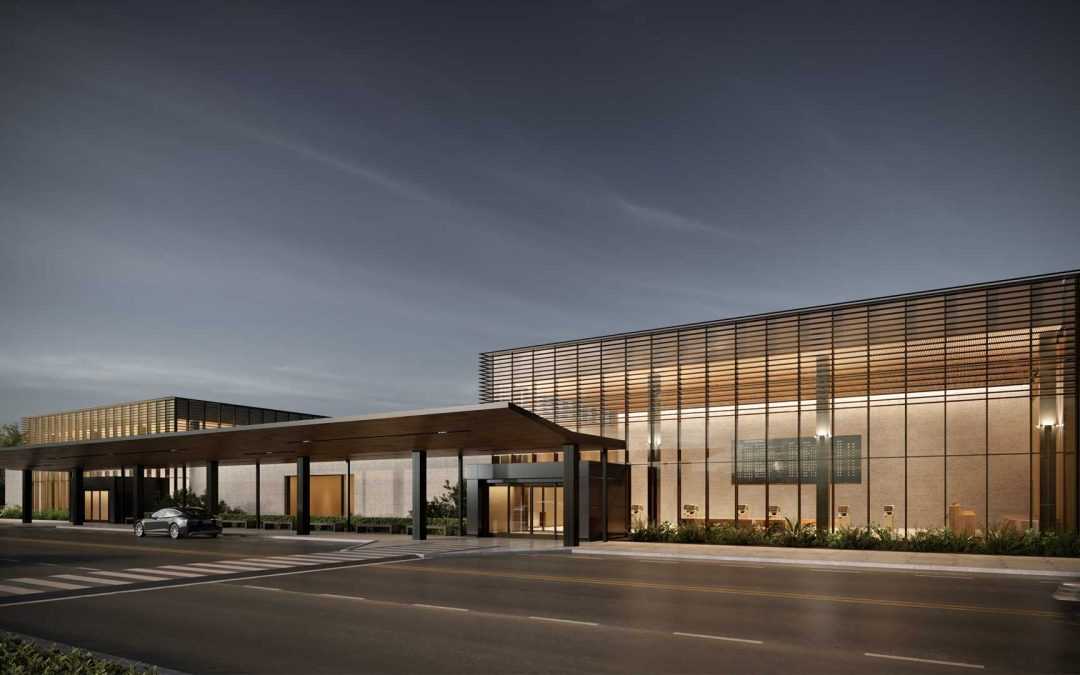
Fisher’s Paine Field Terminal Voted Best Regional Airport in the World
The recently opened Paine Field passenger terminal continues to win awards. Most recently it was voted best regional airport by Monocle Magazine's...
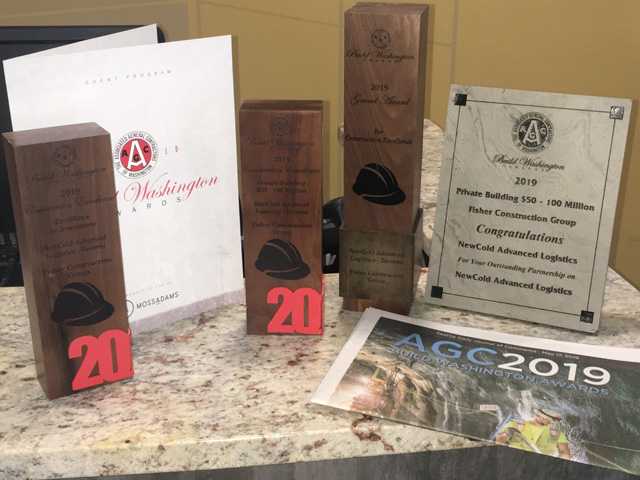
Fisher’s NewCold Project Wins Multiple AGC Awards
Fisher Construction Group earned the Associated General Contractors's Build Washington Grand Award for Construction Excellence for their work on...
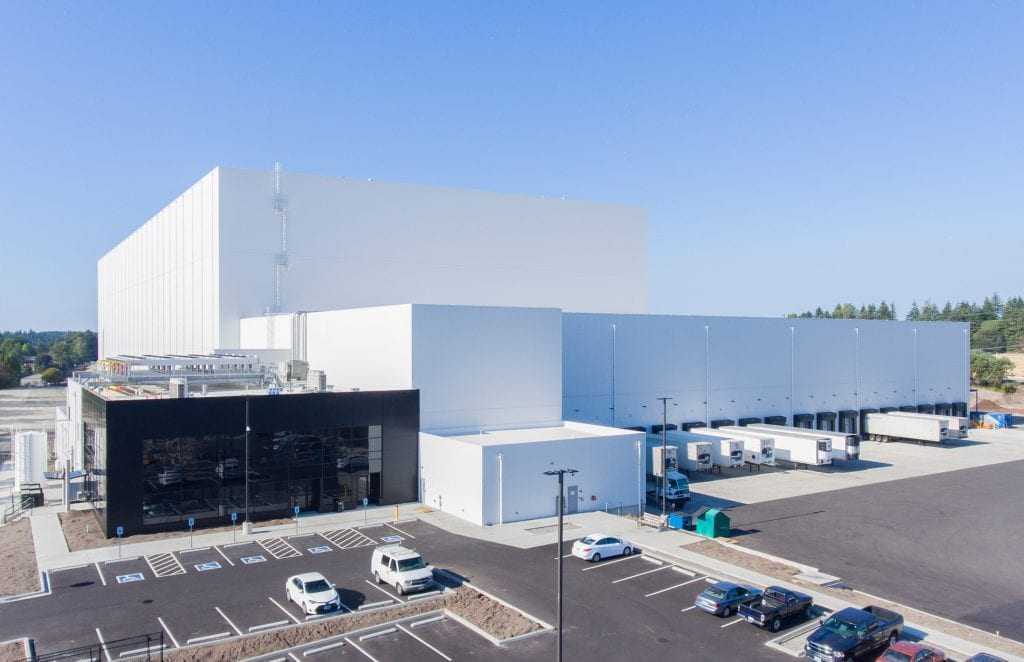
Fisher Wins 2018 Built by the Best Award
Arlington, Virginia, November 26, 2018 – Fisher Construction Group was named the winner of the Controlled Environment Building Association (CEBA) Built by the Best Award for their project with NewCold in Tacoma,...
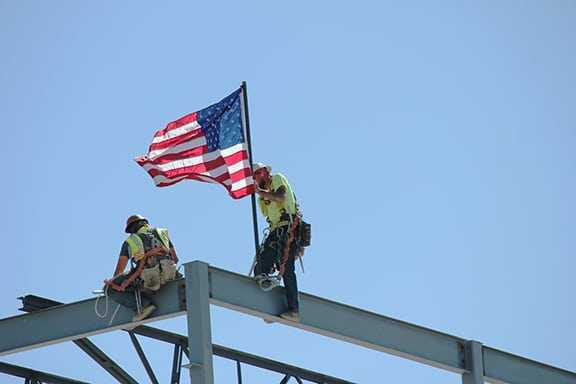
Fisher, NewCold and McCain Celebrate Steel Top Off
Fisher Construction Group, NewCold and McCain Foods joined with many, many fans of Idaho economic development to celebrate the Steel Topping Off of NewCold's second US cold storage. The event celebrated the topping off of the low-bay which will...
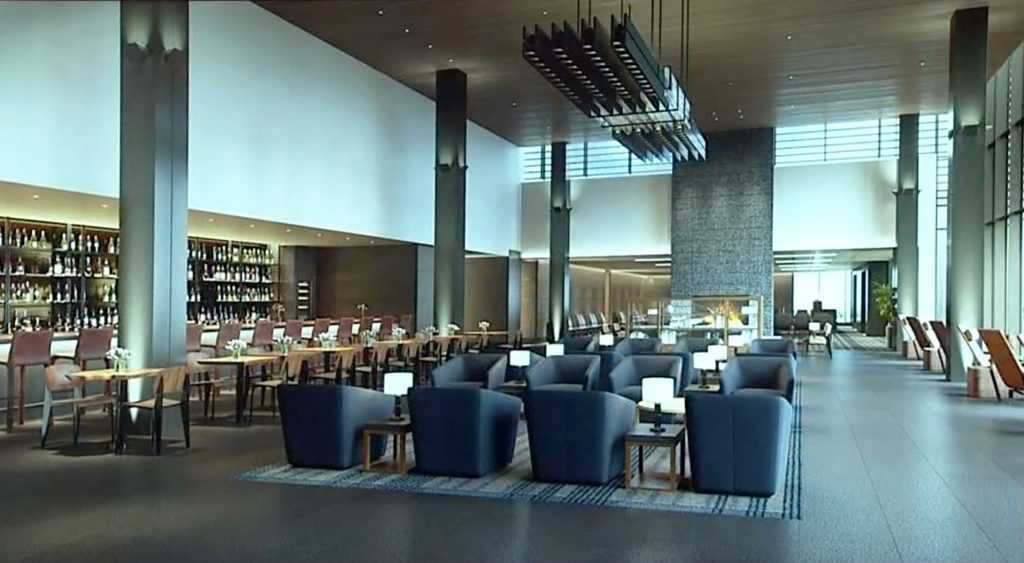
Fisher’s Highly Anticipated Paine Field Terminal Gets Lots of Press
Just type 'Paine Field Terminal' in google and take your pick of news stories featuring Fisher's Paine Field Terminal Project in South Everett. While eliminating a trip through Seattle traffic might have been enough of a draw, Propeller Airports,...
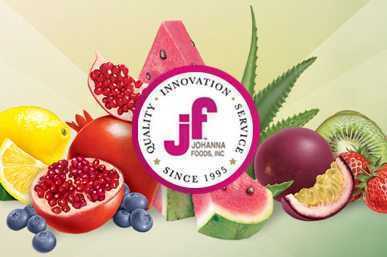
Johanna Beverage Selects Fisher Construction Group to Build New Refrigerated Storage Facility in Spokane
Spokane, WA, February 13, 2018: Johanna Beverage announced today they will break ground on a new refrigerated warehouse at their Spokane facility early this spring. Fisher Construction Group has been selected as the general contractor and will...
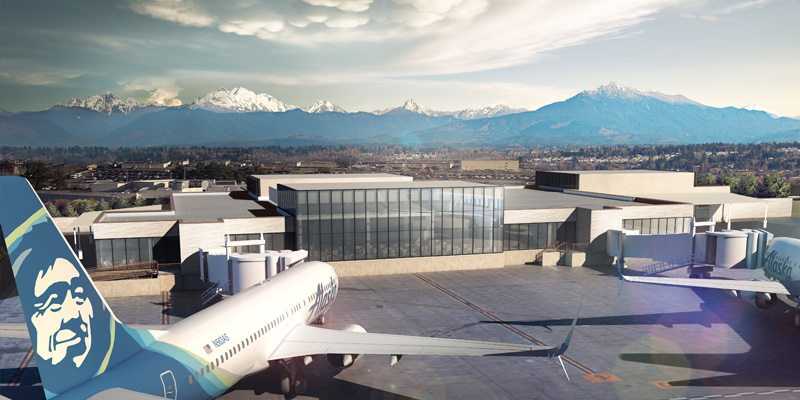
Early boarding pass: Everett’s rising passenger terminal
Here’s what to expect when two airlines begin passenger service at Paine Field later this year. By Jim Davis Published Wednesday, January 10, 2018 HERALD BUSINESS JOURNAL used with permission EVERETT — Brett Smith...
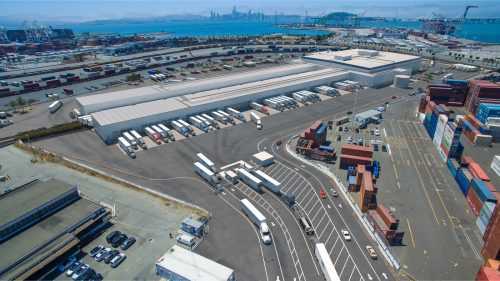
Fisher’s ‘Cool Port’ Project Is Underway in the Port of Oakland
While building a cold storage is complex enough, sometimes the huge amount of planning that occurs before the first excavator arrives on site makes the actual structure that much more amazing. So it is with the...
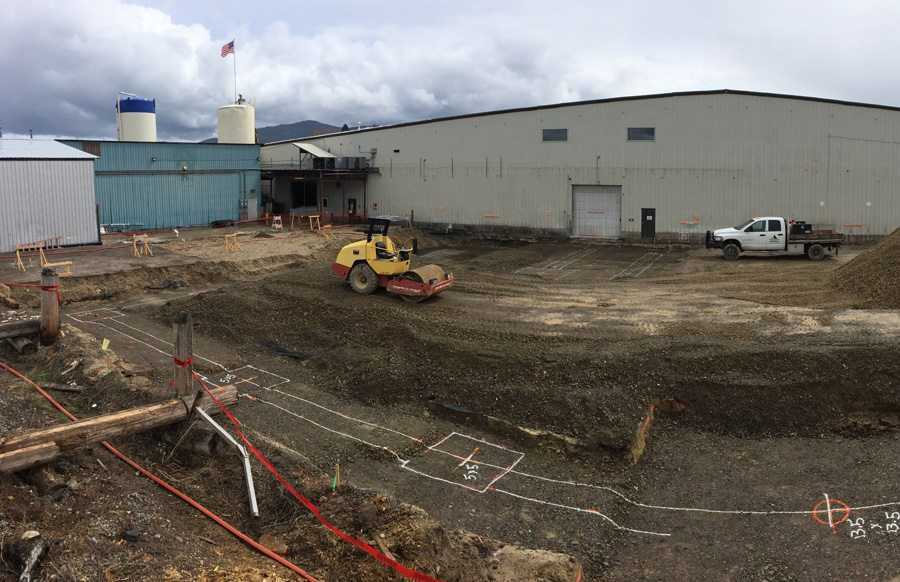
New Project with Litehouse Foods
Fisher Construction Group is pleased to be working with Litehouse Foods on the Ella Cooler...
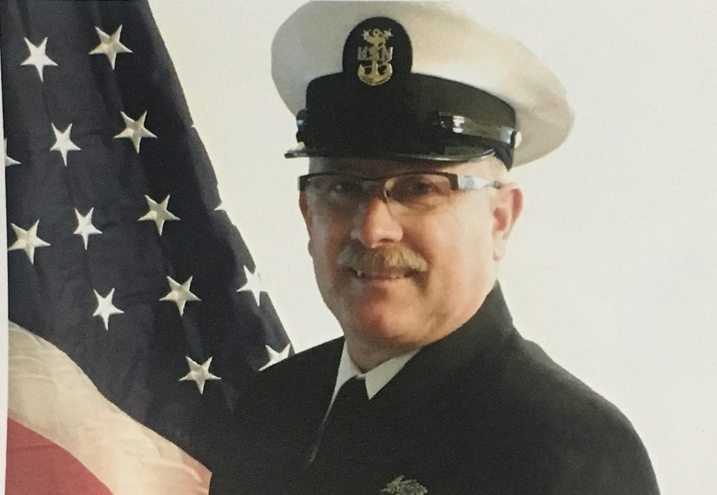
Thank You for Your Service Eric
It’s time to salute Eric Burcroff, one of our own. A Fisher employee since 1998, Eric...
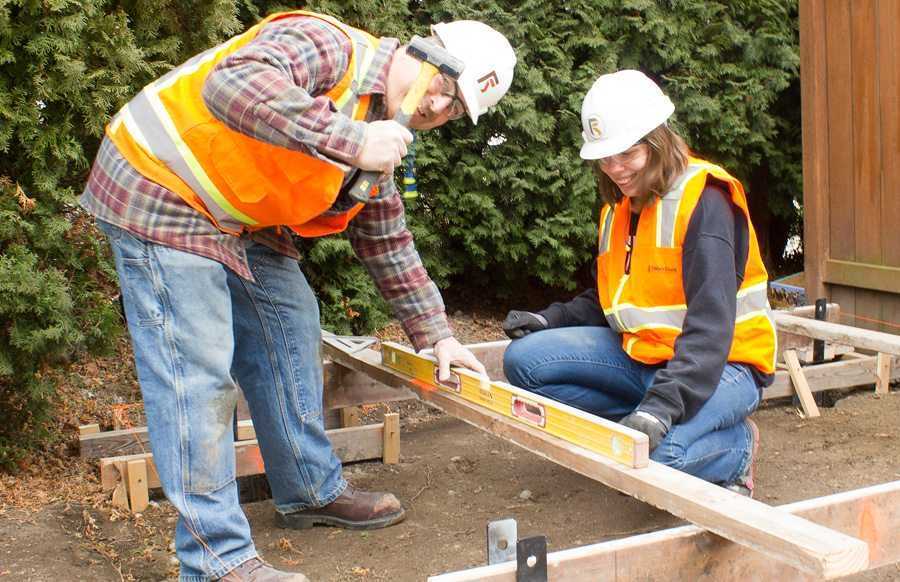
Fisher’s Team Gives Back to the Community
Fisher's Architecture and Engineering team recently built an outdoor shelter for Friendship...
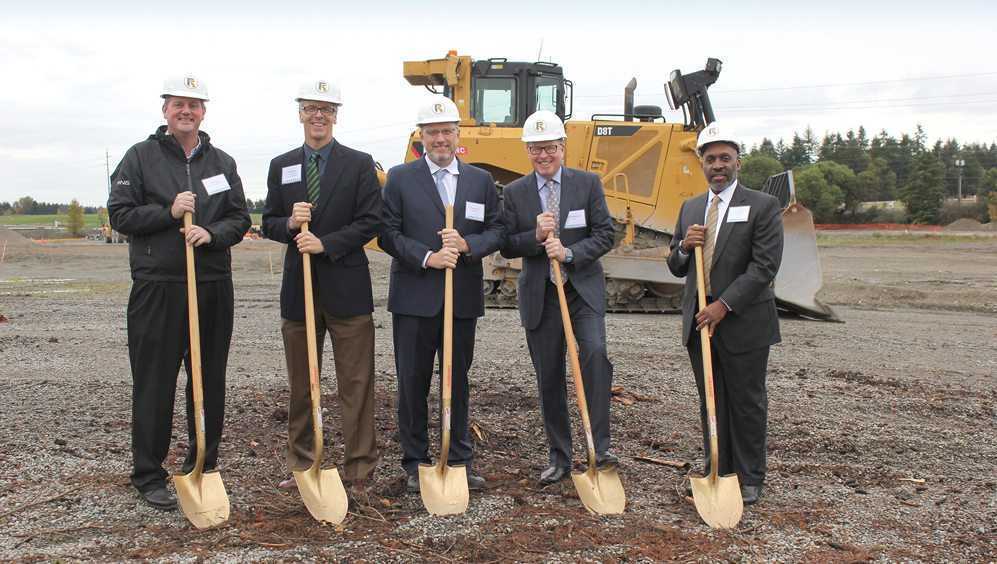
NewCold and Fisher Break Ground in Tacoma
Tacoma, WA, January 3, 2017: NewCold and Fisher Construction Group have broken ground for building NewCold’s Tacoma Automated Coldstore, located in proximity to the Port of Tacoma and I-5. The coldstore will use state of the art technology...
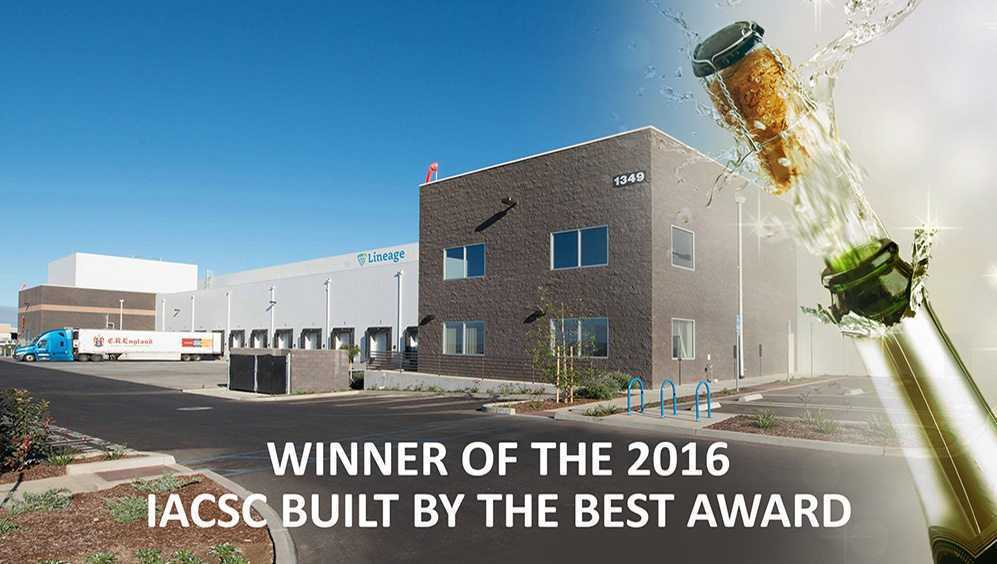
Project Honored with Built By the Best Award
Alexandria, Virginia, November 3, 2016 – Fisher Construction Group was named the winner of the...

Silver Bay Seafoods Nearing Completion
Keeping Pace with Global Seafood Demand Silver Bay Seafoods LLC is a processor of fish products based in Sitka, Alaska. Born out of the vision of a group of fishermen, Silver Bay’s integrated approach to catching and processing fish for domestic...
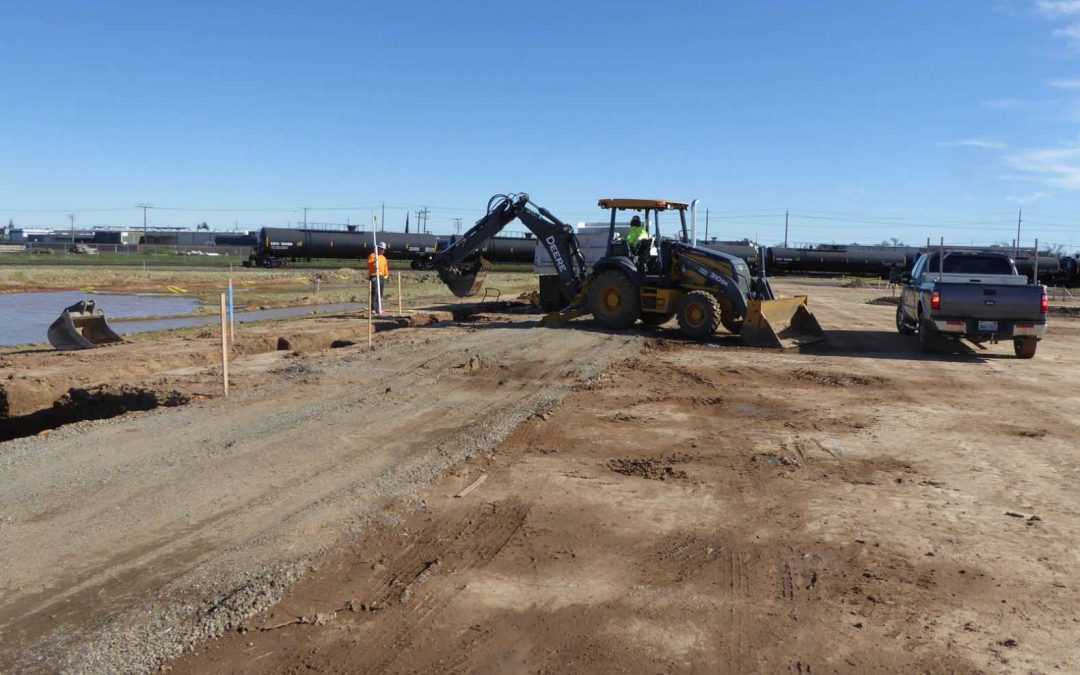
Fisher Breaks Ground for US Cold Storage in Sacramento
While rain in California is very welcome, it seems like much of it has fallen on the 40 acre US Cold Storage jobsite in Sacramento. Since the soil wasn’t draining quickly enough through the original sediment traps, the team resorted to creating a...
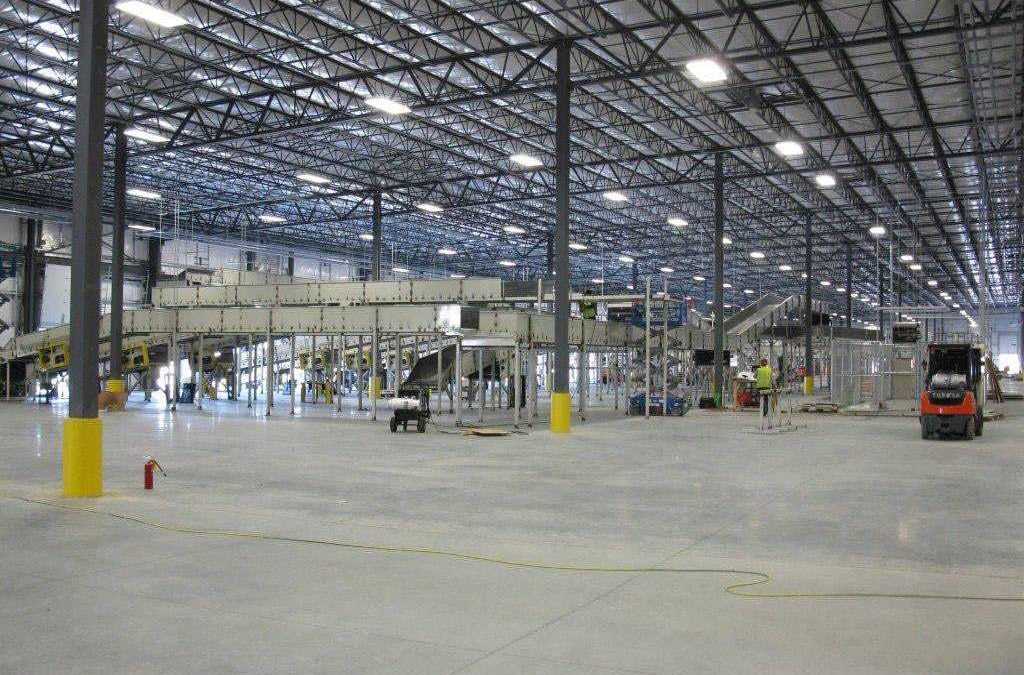
FedEx Distribution Hub Takes Shape
Construction work is progressing on the 220,000 sq. ft. facility in south Burlington. Fisher Construction Group is the general contractor, building the facility for Jones Development from whom FedEx will lease. The ground distribution hub is being...